How to Set Up Your Holster Quality for Exporting Products
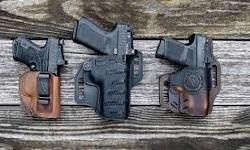
Establishing quality standards is an important procedure for manufacturers and businesses operating in the firearms, ammunition, and accessories sector regarding holsters they would export. Compliance with global quality and safety standards will increase your brand value while reducing the risk of expensive returns, regulatory penalties, and damage to brand capital. In this blog we will discuss the seven steps that should be taken to set up solid QA procedures for holsters going to overseas markets.
Understand the international standards and rules
Before you do one thing to establish your custom leather holsters quality for export, you need to get yourself familiar with the international standards that apply to your products and their corresponding regulations. Some countries may require help with materials, safety, and performance. There are few important things to note, such as:-
ISO Certifications:
International Organization for Standardization (ISO) guidelines can lead to a better quality and safe product. ISO 9001 certification — ISO 9001 is a popular quality management systems standard.
Country Instructions:
Check the guidelines for the nations that you are transporting out to. Other parts of the world might have some local or national standards on the raw materials used in holster manufacturing, or if it needs to be labeled & how (if safety features are even necessary). — Mini and Midsize Holsters for Jilmil Style Handguns
Knowledge of Industry Standards:
Understand the holster standards established by agencies like the National Institute of Justice (NIJ).
Establish QA Processes
Creating solid quality assurance processes is key to delivering consistency in product quality. Here are some key components:
Quality Control (QC) Inspections:
Conduct QC inspections at multiple points along the production process. It involves both checkups on raw materials, in-process inspections and evaluation of final products to make certain that they comply with quality standards.
Standard Operating Procedures (SOPs):
Create SOPs for the different parts of the production process. SOPs should specify the steps to follow, quality checkpoints and documents.
Testing Protocols:
Develop testing protocols to assess the function and longevity of holsters. Look at retention, draw, and wear resistance. Conduct both lab and field trials.
Train Your Workforce
It is important to have a workforce that can maintain quality standards, which requires proper training and knowledge. Engaging events that deliver quality training, focused on:
Quality Standards:
Get all employees educated about the quality standards and regulations regarding holster production and export.
Production Techniques:
Train on best manufacturing process practices, such as material handling methods, assembly techniques, and finishing techniques.
Quality Inspection Practices:
Train employees on how to carry quality inspections and know the defects/issues that might arise during production.
Select Quality Materials
Materials:
The materials that go into any custom leather holster are going to directly impact the way a holster works, and how long it lasts. Consider the following:
Source Quality Supplier:
Collaborate with trusted suppliers to get quality material that meets the safety and performance requirements. Conduct regular evaluations on their performance and quality
Material Testing:
Test incoming materials to verify they meet your specification such tests may be tensile strength, abrasion resistance and chemical resistance tests.
Tracking and Documentation
Well-documented and traceability are vital for quality assurance and compliance:
Production Records:
Maintain production records that provide detailed information about the process – include material batch numbers, inspection results and any deviation from standard operating procedures.
Export Paperwork:
Check efficiency in export paperwork. Such as compliance certificates, bills of lading, and customs declarations.
Feedback And Further Improvements
Create a mechanism for collecting feedback from customers and stakeholders to find potential weaknesses:
Customer Reviews:
Request customers to review the overall performance and quality of your holsters. Do surveys and check reviews but also speak for yourself.
Performance Metrics:
Match up performance metrics as return rates, warranty claims and customer complaints in order to observe trends and areas that need improvement.
Continuous Improvement Programs:
Apply continuous improvement programs, like lean manufacturing or Six Sigma, to improve production processes and product quality around progressions of time.
Audit and Inspection Readiness
Exported product will be audited or subject to inspection if it comes from a regulatory agency or even by your client:
Internal Audits:
Schedule and conduct internal audits of your quality management system regularly to verify compliance with set standards and pinpoint areas for improvement.
Involve third-party auditors to assess your quality assurance processes in an unbiased manner.
Conclusion
Establishing proper quality control standards for export holster manufacture is a complex array of procedures that will need to be carefully planned out, executed, and continually evaluated. Heed these steps and see to it that local holster regulations are understood, quality assurance processes have been placed robustly in place, materials chosen are of good standards and a culture of continual improvement has been developed — your holsters will reach the highest benchmark. Not only does this increase your reputation in the international market, but it also sets you up to gain customer and partner trust around the world. Your business will flourish and can grow bigger in the market of international trade with a focus on quality.