Understanding a Facelift
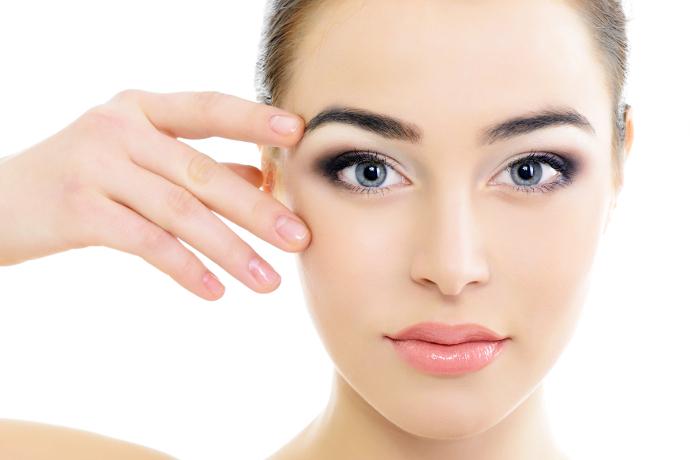
A traditional facelift, also known as a rhytidectomy, is a comprehensive surgical procedure designed to address aging signs across the lower two-thirds of the face and neck. This procedure focuses on tightening sagging skin, removing excess fat, and lifting the underlying facial muscles to create a smoother, more youthful appearance.
During a facelift, incisions are typically made around the hairline, extending down to the lower scalp, and sometimes under the chin. This allows the surgeon to reposition the skin and deeper layers of the face, ensuring a long-lasting result. Facelifts are ideal for individuals experiencing significant sagging, deep wrinkles, and jowling.
The results of a full facelift are often dramatic and can make patients look 10 to 15 years younger. However, this procedure requires a longer recovery period, often ranging from two to four weeks. Bruising, swelling, and discomfort are common during the initial stages of recovery, but these effects subside over time.
What Is a Mini Facelift?
A mini facelift, sometimes called a “weekend facelift,” is a less invasive version of the traditional facelift. This procedure primarily targets the lower face, focusing on mild to moderate sagging in the cheeks, jawline, and neck.
The incisions for a mini facelift are shorter and more discreet, usually limited to the area around the ears. Because the procedure is less extensive, it involves minimal skin and muscle adjustment. This makes the mini facelift a popular choice for younger patients or those with early signs of aging who are not ready for a full facelift.
Recovery from a mini facelift is quicker, typically lasting about one to two weeks. Patients experience less swelling and bruising, allowing them to return to their daily activities sooner. While the results are not as dramatic as a full facelift, a mini facelift offers a noticeable improvement in the lower face and provides a refreshed appearance Facelift vs mini facelift.
Comparing Costs
The cost of a facelift versus a mini facelift can vary widely depending on factors such as the surgeon’s experience, geographic location, and the specifics of the procedure. On average, a full facelift costs between $10,000 and $15,000, while a mini facelift typically ranges from $5,000 to $8,000. It’s important to note that these figures may not include additional expenses such as anesthesia, facility fees, or post-operative care.
Deciding Which Option Is Right for You
When choosing between a facelift and a mini facelift, several factors come into play:
- Age and Skin Condition: A full facelift is generally recommended for individuals in their late 40s to 60s with significant signs of aging. A mini facelift is better suited for younger patients or those with mild to moderate skin laxity.
- Desired Results: If you’re looking for a dramatic transformation and want to address multiple areas of aging, a full facelift may be the better option. For those seeking subtle improvements, a mini facelift can deliver a refreshed and natural look.
- Downtime: If you have limited time to dedicate to recovery, the quicker healing process of a mini facelift might appeal to you.
- Budget: Cost considerations also play a significant role. A mini facelift is more affordable, making it an attractive option for individuals with a smaller budget.
Combining Procedures
In some cases, patients opt to combine a facelift or mini facelift with other cosmetic treatments, such as eyelid surgery (blepharoplasty), brow lifts, or non-surgical options like dermal fillers and Botox. These combinations can enhance the overall rejuvenation effect and provide a more harmonious result.
Conclusion
Both facelifts and mini facelifts offer effective solutions for combating the signs of aging. The decision ultimately depends on your individual needs, goals, and circumstances. Consulting with a board-certified plastic surgeon is crucial to determine which procedure aligns with your expectations and lifestyle. Whether you choose a full facelift for a comprehensive rejuvenation or a mini facelift for subtle improvements, both options can help restore confidence and achieve a youthful, refreshed appearance.